Gen3 Formula E: To Charge or Not Charge?
DECEMBER 21, 2019
The racing format of Formula E provides incredible interest. Like other series, the cars qualify and line up on the grid in descending order of speed, but tight tracks, close racing and energy strategy decisions mean that overtaking is frequent. The right mix of regulations and circuits mean that the result is far from predictable. In fact 9 teams managed a podium position during the 13 rounds of season 5. By way of comparison with FE’s older and more predictable relative, Formula 1 saw only 5 teams share the podium over 21 races this year. It is for this reason we were intrigued to see how things might change with the recent FIA tender for the 2022–2025 Gen 3 FE chassis and front powertrain kit.
250kW Front Harvest-only Motor
The most notable change is the inclusion of a 250kW front e-powertrain regen. This won’t allow four wheel drive, because it provides regen power only. We have run some simulations around Marrakesh to look at the effect of this, along with the other changes to the Gen3 car. The overlay below shows qualifying:
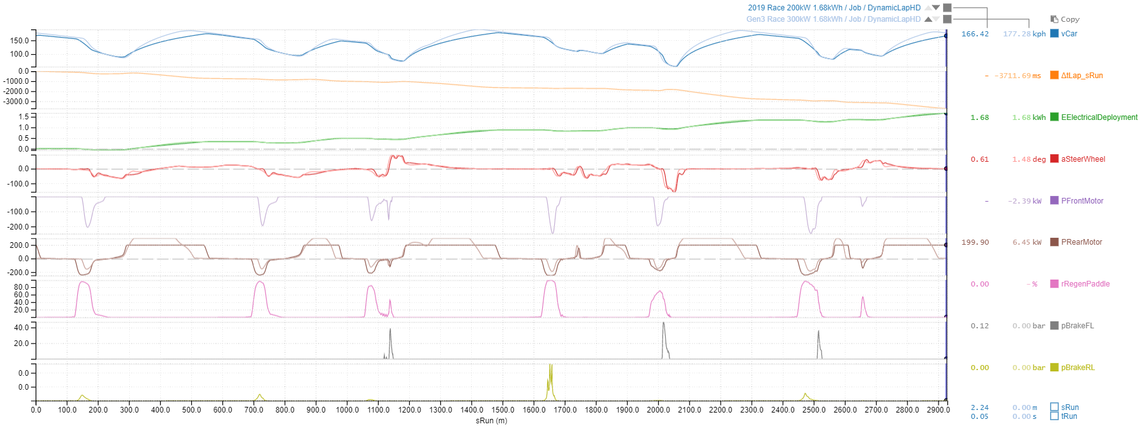
Qualifying Gen2 Season 5 2019 and Gen3 car
The main difference is in the acceleration down the straights caused by the increase in rear motor power from 250kW to 350kW and reduction in weight from 900kg down to 780kg. There are slight differences during braking and corner exit (see Turn 1 in the comparison below) as the more powerful car takes a different racing line to straighten the exits to allow the extra power to be applied. Overall the Gen3 car is 3.5seconds quicker. The rapid acceleration causes it to back of the throttle to make it around the high speed corner shown by the blue marker below.
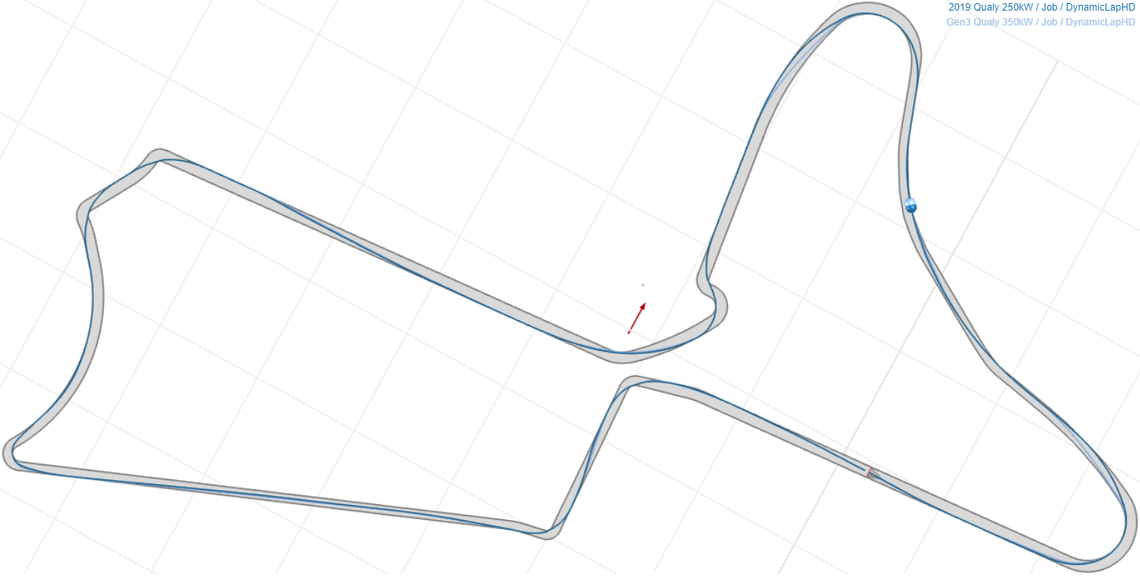
Racing Line Comparison
In qualy mode we can see that even with the extra power, the net energy deployment is reduced by 0.21kWh thanks to the front motor harvest (PFrontMotor). It makes good sense to recover energy from the front axle, because as cars brake, the weight transfers forwards causing an increase in the front tyre load. This gives the front axle more potential for braking.
Another observation is that the rear brakes on the Gen3 car are barely touched (max 4Bar, compared to 130Bar seen on an F1 car) due to the extra motor harvest power available. This is just as well because the Gen3 car might see the deletion of the rear friction brakes and rear brake by wire (BBW) system which applies retardation from the electric motor first before the friction brakes are applied. This is an excellent weight saving opportunity.
Improved Car Balance
With the Gen2 FE car, all energy harvest is done using the rear axle. This leads to a car setup nightmare; on corner entry the car needs as much rear grip as possible to convert kinetic energy into electrical energy. We can see this by looking at the Secondary Lap Sensitivities (SLS) to grip (see “Showing our Sensitive Side” to understand how these work). The channels dTLap_drGripFactorF & R tell us how much the laptime would be improved if we increased front or rear grip at this particular point around the circuit. At the cursor position below (late corner entry), dTLap_drGripFactorF goes negative while dTLap_drGripFactorR peaks for the Gen2 car (in bold). This is telling us that the car is in such desperate need for rear grip in order to maximise regen that it would actually go quicker if we sacrificed some front grip at this point to make the car less oversteery.
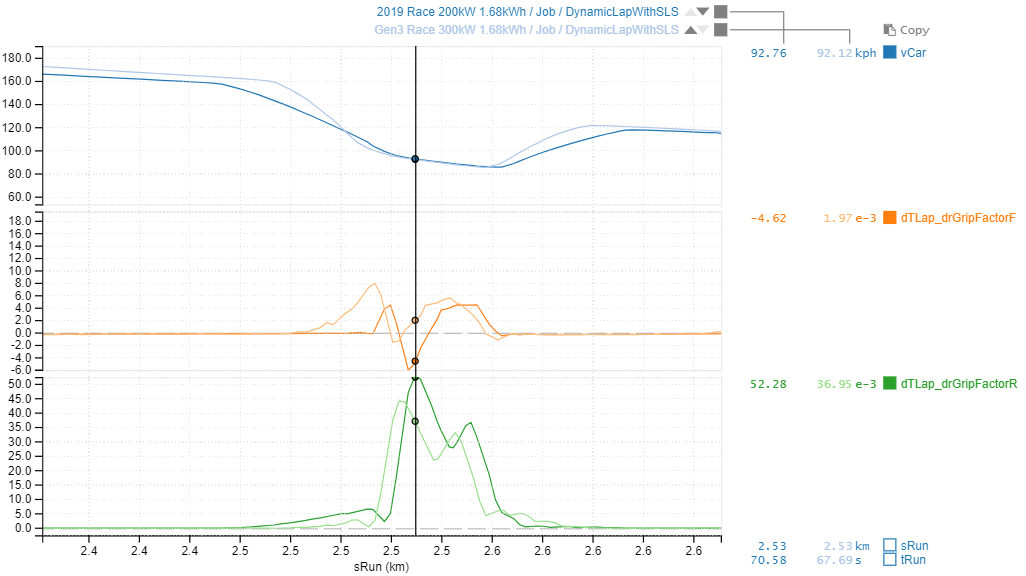
Through corner balance shown by sensitivity to front and rear grip
When the car gets to mid corner, it needs front grip in order to get the car turned. This can be seen by the orange dTLap_drGripFactorF channel peaking at mid corner. On exit, rear grip is required for traction, so the green dTLap_drGripFactorR channel has a second peak
This leads to a car with entry oversteer, mid corner understeer and exit oversteer: a problem known as poor through corner balance and one which frustrates the drives and requires considerable engineering effort to solve (one method of improving it is outlined here in “How to balance an F1 car through the corner”).
Adding front regen means the car is no longer in desperate need of rear grip on entry in order to maximise regen. This can be seen by looking at the fainter lines in the above figure for the Gen3 car: dTLap_drGripFactorF is no longer negative at the cursor position, and our sensitivity to rear grip dTLap_drGripFactorR doesn’t peak as high. While this might look like a small difference on a graph, in terms of driver confidence if the rear is trying to break loose it stops the driver being able to attack the corners as hard.
Removal of the Regen Paddle
It is this change that we are most excited about. To explain why, first we must understand why the Gen2 cars have a regen paddle. To complete a race with limited battery capacity, the optimal energy deployment found by Dynamic Lap is shown below for 1.68kWh net deployment per lap (the energy level required to complete 31 laps of Marrakesh race with a 52kWh battery):
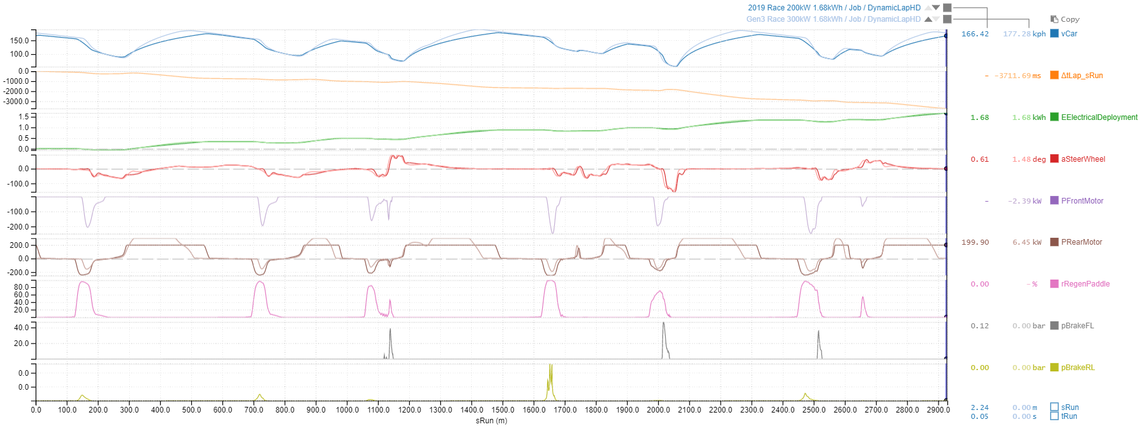
Race Gen2 Season 5 2019 and Gen3 car
The optimal deployment strategy can be broken down as follows:
Accelerate as hard as you can out of the corner.
Lift off the throttle near the end of straight to save energy (PMotor drops to zero, and car slows gradually).
“Braking” is then performed in two steps:
Pull the regen paddle (rRegenPaddle) to recover electrical energy from the rear axle and start slowing the car.
Use the brake pedal for the final part of retardation to apply the front brakes in order to get the correct corner entry speed.
It is an annoyance for drivers and engineers alike to split braking into two phases. With the Gen2 car teams have to do this in order to maximise energy recovery. Any energy that goes into the front friction brakes is wasted as heat so the front brakes are only used in the final few meters before the corner. This is a crazy situation because drivers are using the regen paddle to do the majority of braking instead of the actual brake pedal which is only used in the second part of braking to finesse the final car speed.
By adding front regen, the Gen3 car gets rid of the need for a regen paddle. The brake pedal is wired up to both the front and rear motors which are applied simultaneously. There is no longer a need to use the rear regen first, followed later by the front brakes, because both axles now recover energy so nothing is wasted by applying them together (assuming they have similar efficiency). This means that drivers can brake harder using both axles allowing them to attack the corners, and more importantly they can use the actual brake pedal to do this. Good riddance to the regen padle!
30sec Charging Pitstop
As part of the tender, the spec includes the provision to do an optional pitstop for 30sec of fast charging. We were keen to simulate whether it is better to use more energy then stop to recharge, or conserve energy and stay out on the track.
First we need to makes some assumptions about the battery capacity and charging rate. The current technical regs state a 280kg maximum battery weight, while the target weight for the new battery is 284kg. The increased charging power might put additional demands on the battery in terms of heat dissipation and cooling, so for argument sake, let’s assume a similar race energy limit of 52kWh. Since the battery system is designed for 350kW regen from the rear axle and 250kW from the front, i.e. 600kW total during racing, we assume that pitstop charging would occur at a similar rate. Some power would be lost to battery efficiency, and rounding down for simplicity means that teams can top up their cars by 4kWh.
If we run an energy sweep, we can see how the laptime varies for different levels of energy saving. The current race format is 45min + 1 lap. We can use the laptime at each energy level to calculate the number of laps (plus 1) that can be completed(NLapsTimeLimit). We can also calculate how many laps can be completed at this energy level before the battery runs out (NLapsEnergyLimit). Where the two lines meet in the figure below (at the cursor) represents the quickest the car can be driven without that battery running out. Without a pitstop it can complete 34laps with the Gen3 car (3 laps more than at Marrakesh this year):
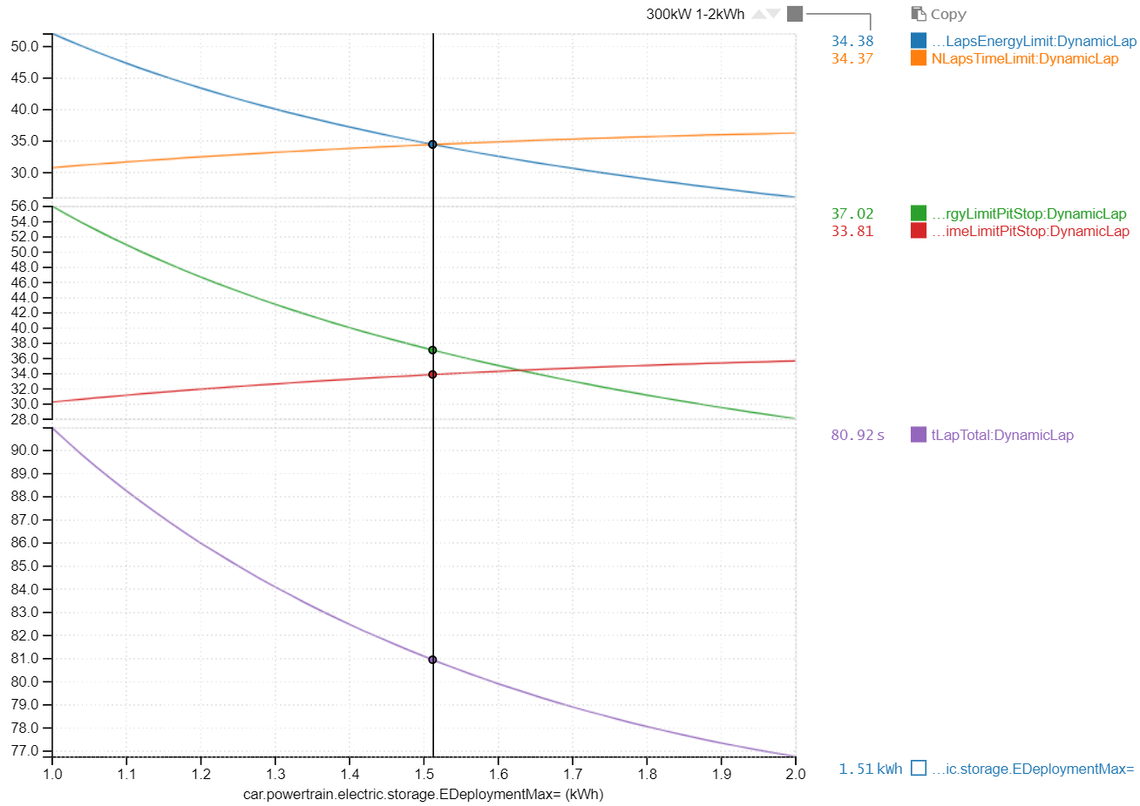
Sweep of energy per lap showing laptime and number of laps possible
To look at the pitstop scenario, let’s assume that for Marrakesh the pitlane time loss (versus staying on the circuit) is 15sec, so cars would lose a total of 45sec by stopping to charge. If we repeat the NLapsTimeLimit (red line above) calculation with 45sec taken off, and add 4kW to the NLapsEnergyLimit (green line) calculation then the curves intersect again at 34laps. It’s too close to call so we need to drill down into the laptimes.
With no pitstop, the best laptime for 34laps is 1m20.71s. With the extra energy from a pitstop this improves to 1m19.40s i.e. 1.31sec faster. Over a 34lap race the stint time with pitstop is 44.54sec quicker, however if a pitstop takes 45sec, then it will be a very close call indeed.
Is there anything to watch out for?
Overall we think the changes represent a big step forwards in terms of racing, simplicity and developing road relevant technology. All those involved at the FIA and FE teams in shaping this specification deserve to be congratulated for designing what appears to be a well thought out future. There are a couple of things that we would keep an eye on; with 300kW motors, the cars consume energy much quicker so the drivers have to lift off the throttle earlier (around halfway down the straight). Perhaps this is why the tender includes a scenario B for 250kW rear motors which would run for longer down the straights. Teams might also have to watch out for battery overheating with the massive increase in power going into and out of the battery. As well as balancing energy usage, battery thermal management might once again become a crucial part of the championship battle.
The spec is likely to evolve as the various tenders come in and it becomes apparent what is possible from a technological standpoint. We can’t wait to find out what will happen, and will be ready to provide simulations to FE teams to arm them with the knowledge required to extract maximum performance from the Gen3 cars.