Front, Rear or All Wheel Drive at the Nürburgring Nordschleife?
OCTOBER 25, 2017
There appears to be no slowdown in the relentless battle of auto manufacturers chasing down Nürburgring laptimes in order to gain a top spot at the ring and prove their engineering prowess. With a variety of cars running sub 7 minute laps we asked ourselves which powertrain configuration is fundamentally quickest around the green hell; front, rear or all wheel drive? Few would gamble on a front wheel drive being quickest, particularly at the ridiculous power level we’re testing at, so let’s put some numbers to it and find out. We’ll also take a look at the benefits of adding in torque vectoring — a task which becomes easier with electric cars as there are better opportunities to drive the wheels individually.
First, we need a model of a powerful supercar so let’s make up some specs, and try not to get too carried away!
Weight: 1750kg (about the same as a Porsche 918 with a passenger)
Powertrain: 1MW/1341bhp (a little shy of a Bugatti Chiron)
Downforce: 900kg at 260kph (50% more than a McLaren P1)
Of course, car manufacturers spend years fettling the balance of their car, but since this is hypothetical, we’ll stick with getting the basics right, that is:
Weight distribution (while adjusting spring stiffness to suit).
Aero balance (while matching ride heights).
Mechanical balance (while maintaining total roll stiffness).
We’ll allow the car to have automatic control over the brake balance.
For the 4WD car we’ll optimise percentage torque split to the front/rear.
We ran 10,000 combinations of the above setups around the Nordschleife — a task which is easy to say, but even amongst F1 teams, this is only feasible for the ones using Canopy. Here are the results:
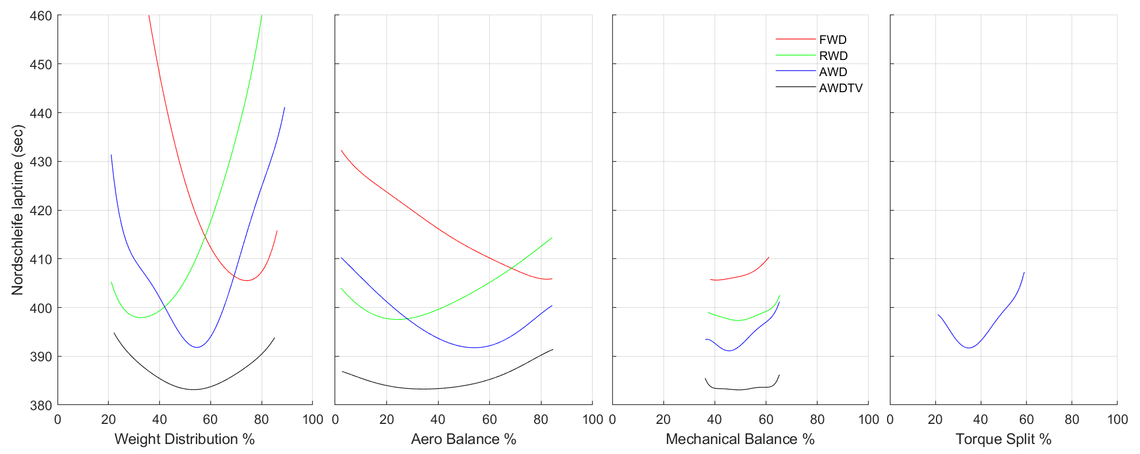
Figure 1: Nordschleife laptimes (bottom) and variations with setup (top)
Let’s take a look at the laptimes first. At this track grip level, the optimal RWD car is 7.6sec quicker than FWD. AWD then gains us a further 6.1sec, while AWDTV widens the gap to a further 8.7sec quicker than AWD. While we pause on this observation, I can hear our FWD fans complaining that drivability is important, and if we were to enter this car into a gentleman’s driving series such as the VLN or the 24 Hours of Nürburgring it is the ease of which we can knock out quick laptimes with metronomic precision that is more important than theoretical ultimate pace. One thing we could do to check the drivability is to see what happens when things get a little damp by dropping the track grip by 10%.
Fortunately, it only takes a few clicks and a cup of tea to re-run the 10,000 simulations to find out. If you work at a motorsports team you’ll know that being able to quickly respond to changing conditions at the track is crucial for racking up those championship points! With the best user interface, most powerful simulations and cloud computing it’s easy to adapt to track layout changes, local grip variations, or wind changes. With the new simulations run we find the laptimes and optimal setup as follows:
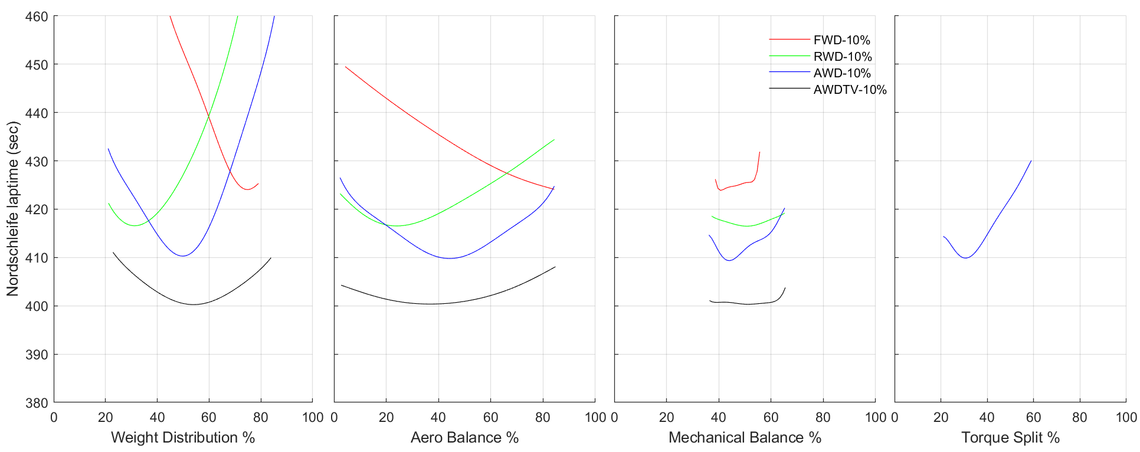
Figure 2: Optimal laptimes and setup with 10% less track grip
The pace difference between the FWD, RWD and AWD configuration is almost identical after a drop in grip, however the interesting result here is that AWDTV performs even better on a damp track relative to the others and has widened the gap by a further 1.4sec.
If we take a look at optimal weight distribution, we can see that weight distribution is by far the most sensitive parameter, as laptimes deteriorate rapidly when we move away from the ideal setup. At the high grip level, the FWD is quickest with 74% of the weight on the front axle (which explains why we don’t see many rear engine examples!), while Porsche owners will be delighted to see that the RWD is quickest with the weight as far back as 33%. BMW drivers with their 50:50 weight distribution could use this graph as an excuse to upgrade to all-wheel drive technology, as 53–55% is ideal for AWD performance.
The aerobalance optimum looks to be very extreme. FWD and RWD demand very far forwards and rearwards aerobalance respectively. I’ve never driven a car with 84% aerobalance around a high speed corner in the damp, but the thought of it sounds terrifying (maybe this explains why I make cars go quicker through engineering rather than driving!) If we impose a stability constraint, the aerobalance is still really far forward, probably because having to steer and drive the same set of wheels puts all the hard work at the front. If this doesn’t line up with our trackside experience (of 1MW FWD cars!), it’s really easy to adjust the setup. We can do this in the Canopy user interface by dragging the aerobalance rearwards to what we feel is a more acceptable balance and then moving the weight distribution and mechanical balance to their new optimum.
Mechanical balance has the smallest effect, which is good to know as it leaves the race engineer free to adjust this in order to tune the balance to driver preference without having a detrimental effect on ultimate performance.
In the case of the AWD where we have a fixed % front/rear torque split we find that 35% front/65% rear is a good place to start, with steep loss in laptime when we start to move away from this point. The ultimate solution is to have a dynamic front/rear and left/right split, as is the case with AWDTV. Perhaps the most significant result here is that by opting for torque vectoring, not only do we leave the other cars in the dust, but we are much less sensitive to weight distribution, aero balance and mechanical balance. This brings with it two major advantages: 1) it is much easier to design a car when we’re not restricted to keeping the design within a very narrow window 2) it’s probably much easier for the driver to consistently exploit the performance if the car performs well over a wider range of setups.
Now I can hear our RWD fans complaining that the equipment used to run AWDTV with a standard ICE is heavy. By adding weight to this car, we find that it takes 680kg to bring the performance down to the level of the RWD. This partly explains why the Porsche 918 is so quick around the Nordschleife while boasting more most modest headline figures when compared to the current crop of hypercars. With so many corners to get right, drivability has to be prioritised here.
The results seem clear; if you want to go fast and have a car that’s not too sensitive to setup, you need all wheel torque vectoring. In reality that’s easier said than done. Our simulations simply have 4 throttle and brake controls — one for each corner of the car; maybe a realistic aim if we’re making instruments for a one man band, but less practical when we’re trying to drive on the limit for 7minutes at an average speed of 215kph.
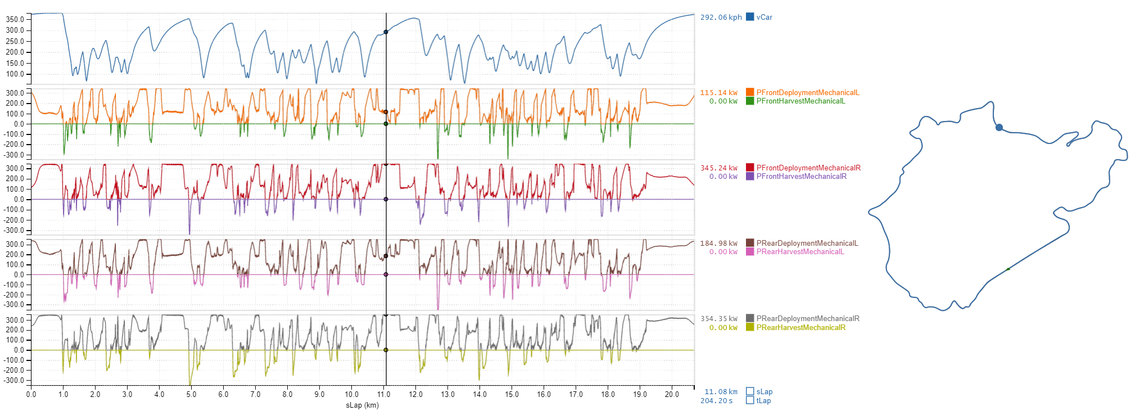
Figure 3: Optimal four wheel torque vectoring
Dynamic lap has no built in torque vectoring strategy; the only objective is to generate a perfect laptime — this is the only way to guarantee optimality. We can look through this perfect lap and identify features from Figure 3 which help us design a strategy, for example applying torque to the wheel with the most grip or providing more torque to the outside wheels while braking the inside ones to produce a yawing moment.
The challenge is to design a system that can take a single throttle & brake pedal then intelligently distribute the torque between the four corners. To help with this we could embed the controller logic within the Canopy platform. In the same way as we swept through setup parameters in this exercise, we could sweep through control parameters for the torque vectoring controller. This would help us to quickly develop a system which gets close to the perfect torque distribution. An alternative way to get closer to perfect torque vectoring would be to remove both the driver and controller strategies altogether and run the car autonomously, with our vehicle model running live in real time on the ECU. Maybe that would spoil the fun!
If you’re a motorsports engineer and you would like to optimise the behaviour of your torque controller; or maybe you are tired of inefficient work flows and can’t simulate 20,000 laps around the Nordschleife in a few hours, then we’d love to discuss how we can help. Send us a message at hello@canopysimulations.com