2017 Aero Regulations meet 2014 Powertrain Regulations
JANUARY 30, 2017
Back in 2013 power deployment in F1 was a big deal. The new powertrains due to appear in 2014 required harvesting electrical energy from a turbo and under braking, then working out exactly where that energy should be fed back to an electric motor to get the best possible lap time. Alongside this, under the new regulations, we also needed to optimise the use of only 100kg of fuel (compared to about 150kg the previous year).
This was a great time to work in simulation in F1, because we were sure that anyone doing a good job of deploying their energy was going to crush those teams who hadn’t invested the same energy and brain power in solving “The energy deployment problem”.
For a while, and certainly in the first half of 2014, this was partially true. Although deployment for much of the grid converged on similar strategies, there was still valuable lap time to be found at each race by trading between:
a) Charging the battery directly from the engine at “part-throttle”.
b) Lifting and coasting into corners to save a bit of fuel.
c) Adopting a lower drag aero-configuration to get you down the straights quicker, thus burning less precious fuel and electrical energy.
However, in F1 “if you stay still you go backwards”, and by the start of 2016 almost all teams could run flat out in both qualifying and race conditions (excepting the need to nurse the tyres). Fuel saving is no longer the big deal it was, and the difference between a poorly executed energy deployment strategy and a perfectly executed strategy is now measured in hundredths of a second, rather than tenths. Mercedes and their ilk have once again done such a good job that the teams using their engines can go back to worrying about aerodynamics without the waters being muddied by the powertrain.
Given this tremendous progress, it was with considerable interest that we started to consider the effect of the 2017 aero regulations. We’re not aerodynamicists, but just a quick glance at the aims of the regulation changes (cars to go 5s per lap quicker than in 2016), and the new aero layouts of the cars gave us a great deal to think about. If you’re unfamiliar with the 2017 regs, then here are the main changes, and the primary effects each will have:
1. Wider car by 9% (increased cornering capability)
2. Bigger and 25% wider tyres (more grip, more drag)
3. Increase in car mass by roughly 25kg (slower acceleration in straight line)
4. Aerodynamic changes: A bigger floor, wider front and rear wing, wider sidepods (more downforce, more drag)
Ultimately we think that these changes could add 25% more downforce and drag at the start of the 2017 season. As teams develop their car through 2017 we may see up to 50% more downforce and drag. Added to this is the increase in tyre grip, we expect cornering speeds to be much higher, and end-of-straight speeds to be lower. So why, given the massive changes wrought by these regulation changes, are we focusing this article on energy usage, for which the regulations remain unchanged?
The answer is that we believe that regulation changes will mean that how energy is harvested and managed will start to take on a much higher significance. As things stand, the majority of the energy deployed by the electric motors is harvested either from the turbo (the MGUH), or through regenerative braking (MGUK), and it is the second of these where we run into trouble with the new regs.
Effectively the amount of energy you can harvest under braking is closely related to the length of time you are braking. If you brake into turn 1 at Barcelona from 341kph to a 123kph you get a 2.2sec worth of harvesting at 120kW. Do this enough times around the lap and you hit the regulatory limit of 2MJ harvesting. Now, at the risk of blinding readers with a flash of the obvious:
a) If you add drag, you go slower at the end of straights.
b) If you add downforce and grip, you go faster around the corners.
Both of these factors reduce your opportunities to harvest energy, simply because the amount of braking time required is reduced. With our 2017 simulation, we now find ourselves braking from 319kph down to 135kph in only 1.6sec. In fact, some corners which were once places to harvest a bit of energy will now be run at 100% throttle, meaning that not only do you not harvest any energy, you are actually spending the energy you’ve got. As the Good Book says “As ye sow, so shall ye reap”, and it’s clear that you can’t deploy energy you haven’t harvested. Furthermore, the main straight which in 2016 took 13s to cover, might now take 14s to cover (due to the additional drag) and this means that all of a sudden, where you choose to stop running your electrical motor will be a big deal both strategically, tactically and from the perspective of overall performance.
Figure 1 shows three features which contribute to the energy issue:
At turn 9 and turn 11 in the 2016 car, the driver has to lift off the throttle. With the 2017 cars we are now at 100% throttle in these corners. This uses more fuel and represents another place where we could deploy MGUK. It also robs us of an opportunity to do part throttle harvest.
The driver no longer needs to brake for turn 9 which loses us MGUK harvest.
At the end of straight into turn 10, the 2017 car is going slower and can brake later which costs us MGUK energy harvest time.
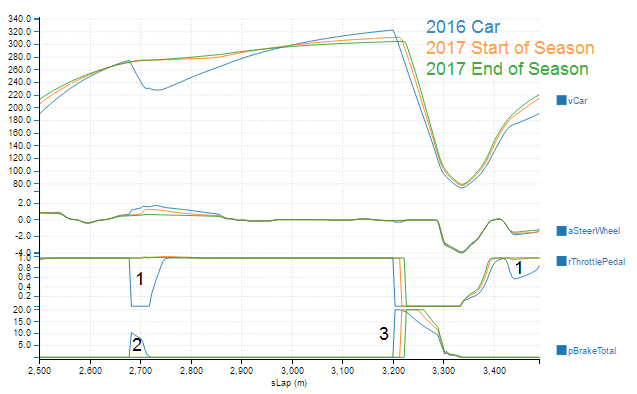
Figure 1: 2017 vs 2016 overlay of Barcelona Turn 9, 10 & 11.
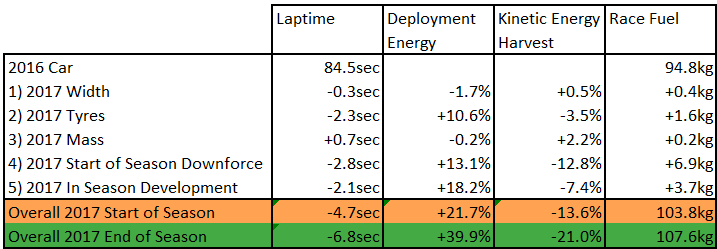
Figure 2: Barcelona circuit simulation: Breakdown of 2017 F1 regulations change.
The numbers simply don’t balance; we can’t consistently deploy more energy than we’re recovering. Worse still, when we consider the potential for aerodynamic development through to the end of the 2017 season (highlighted in green); we realise that we cannot achieve the potential 6.8sec improvement in laptime because we’ve discharged our battery a couple of laps in and emptied our tank with more than one lap to go.
Fortunately for us we have an advanced optimiser which models the complexities of powertrain energy flows. In our DeploymentLap tool we tell the optimiser to match our deployment level to our harvest level, enter our fuel limit, and then press Go! We can see the results in Figure 3.
The bold blue line shows the car speed if we go flat out in qualifying mode. The faint line shows the result of the energy and fuel optimisation which would be required to drive optimally to the end of the the race. The interesting features demonstrated by DeploymentLap are:
Part throttle harvest: the driver is unable to go full throttle at this point around the circuit, so we harvest excess engine power (PERSMotorHarvest) and store it in the batteries for later use.
MGUK deployment: after we get to full throttle, the electric motor is energised (PERSMotorDeploy) to improve acceleration for the first 106m of the straight. It is then turned off to save energy as the optimiser has elected not to spend a excessive energy accelerating when we’re about to brake for the next corner.
Turbo compounding: on the straight we harvest waste exhaust energy through the motor-generator unit connected to the turbo (MGUH: PTurboHarvest). This is fed to the wheels through the MGUK and helps make up for the reduced kinetic energy harvest.
Lift and coast: the driver lifts off the throttle pedal 3m early before turn 7 and coasts down before braking. This is the most laptime efficient way to save fuel. In reality we couldn’t get the driver to perform a 3m lift and coast, so we would consolidate the lift and coast into just a few places around the lap.
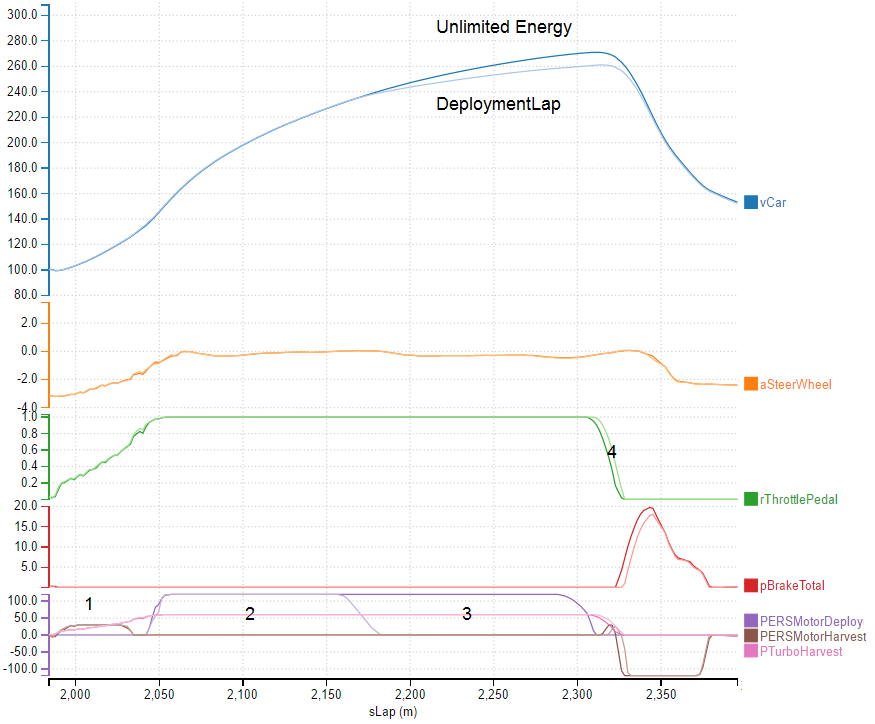
Figure 3: Optimising 2017 Energy use in DeploymentLap. Barcelona Turn 5 to 7.
DeploymentLap tells us that these changes mean there will be about 0.5sec difference between running flat out on the electrical motor and engine, and running in such a way that you don’t empty your battery and run out of fuel. This 0.5sec is worth getting excited about, for a number of reasons:
The difference between bad deployment and good deployment will mean a lot of lap time. Drivers can choose to gain a huge lap time benefit on one lap (perhaps to overtake), but will have to carefully build up their energy reserves again on the next few laps, making them vulnerable to being overtaken.
The interaction between aero and powertrain will be more complex than ever, and aero departments will have to carefully balance the demands of generating downforce against the downsides in terms of fuel and energy use. If you choose to simulate anything to do with the engine, turbo, battery, downforce or drag, but neglect the need to optimally deploy energy then you run a significant risk of leading yourself up the garden path. For example we can quickly compute the isochronal ratio for the two cases (the lift/drag ratio for laptime neutral upgrades; see Aerodynamic Upgrades Facilitated: Isochronal Ratio). The isochronal ratio for the unlimited case ignoring any energy or fuel consumption requirements is 1.8, while for the optimal race deployment the ratio is 1.9. Teams with the tools to optimise energy deployment may end up in a very different place to those who don’t; designing to the wrong isochronal ratio, for example, may cause teams neglecting energy deployment to fit aerodynamic upgrades which have 6% too much drag.
Finally, of course, being enthusiastic simulation writers and proponents, we love the fact that being able to optimise energy deployment for every simulated lap is going to be a big deal. With huge performance gains at stake we can’t wait to see how the various teams approach the energy challenge posed by the 2017 regulations, and how this plays out over the racing season. While we wait for this to happen, here is the full 2017 versus 2016 overlay in all it’s glory, complete with optimal energy deployment:
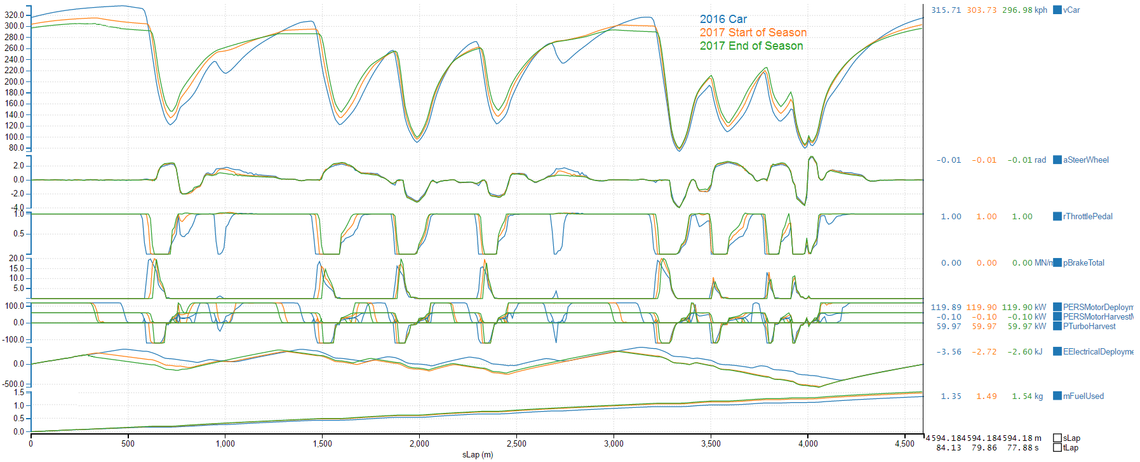
Figure 4: 2017 vs 2016 overlay of Barcelona with DeploymentLap energy optimisation. High speed Turn 9 (sLap = 2750m) should be fun!
For further details on fuel saving see: Fuel Saving: There are no Rules! If you are interested in finding out more about Canopy Simulations please contact us at hello@canopysimulations.com